The tensile strength of rubber is a very important factor that determines the quality of the polymer chosen. Tensile strength tests are also part of quality checks to determine whether a finished polymer product is of expected quality.
Tensile strength determines how much load rubber can handle before breaking up or getting damaged. As someone using rubber components, you should be aware of the tensile strength of rubber to ensure your machinery or part works according to specifications.
What is Tensile Strength?
By definition, it is the maximum force that a material can handle (rubber, in this case) before it breaks down. The unit of tensile strength is pounds per square inch (psi). The tensile strength can also be denoted as Mpa (Megapascals).
Different types of rubber have different kinds of tensile strengths, and manufacturers may be asked to choose the type of rubber depending on the strength they need.

Why know the Rubber Tensile Strength?
Rubber is a flexible and moldable material. When you keep putting pressure on the material, after a point in time, the fibers of the material will break, causing damage. Knowing the tensile strength of rubber will help in knowing the exact point at which this breakdown will occur.
There are three basic types.
- Yield strength – This is the maximum force the rubber can handle without going through permanent deformation. For instance, when a rubber band is stretched to a particular point and left free, it returns back to its original shape. That’s the yield strength.
- Ultimate strength – This is the tensile strength of rubber very close to the breakdown point. Any force beyond this may cause breakage of the material.
- Breakdown strength – This force will cause permanent deformation or damage to the rubber material.
How Does Tensile Impact Product Performance?
Multiple rubber components like valves, seals, and diaphragms may be used in machinery. These components play several roles, including sealing, friction reduction, leakage protection, or vibration suppression.
One inferior quality rubber seal with low strength may cause hazardous leakages and harm people and property in a matter of seconds. A low-strength valve may get damaged and break down when there is an inflow of erosive fluids, leading to productivity loss.
Let’s consider a simple rubber valve fitted in tires to control air pressure. The valve must handle the internal air pressure for it to work for long. Air valves with low strength may need to be replaced more often, bringing down the quality of the product.
Finding the Tensile Strength of Rubber
Two common test methods are used in finding the tensile strength of rubber.
- Dumbbell cut-out method – In this method, a small piece of the sample rubber is cut into the shape of a dumbbell. The cut-out should be between the thicknesses of 1.3 mm and 3.3 mm. The sample will now be stretched until it breaks. The force applied and the elongation shape will be noted down, and the tensile strength will be calculated.
- Ring cut-out method – This method is similar to the first method except that the sample will be in the form of thin rings. These rings would be stretched, and the force applied and elongation shape will be noted to calculate the tensile strength.
How Does the Rubber Strength Vary Between Different Types of Rubber?
The physical properties of different types of rubber change their tensile strengths too. The polymer chains and the crosslinks that make up a material decide how strong the final rubber will be.
Synthetic rubber can be created using a mix of different polymers and additives to make them exceptionally strong and of high tensile strength of rubber.
The following are the tensile strengths of different types of rubber, as marked by Arvico Rubber experts.
Types of rubber | Tensile Strength in Mpa |
Natural | 22 |
Nitrile | 13 |
HNBR | 22 |
Neoprene | 14 |
Hypalon | 20.3 |
Butyl | 17 |
EDPM | 15.2 |
Silicone | 10 |
Viton | 10 |
Polyurethane | 14 |
PTFE | 31 |
As you can see, PTFE rubber (Polytetrafluoroethylene rubber) is the strongest in terms of tensile value. Natural rubber also has a good tensile strength of 22. Materials like silicone, Viton, and nitrile fall under the bottom three in terms of tensile strength.
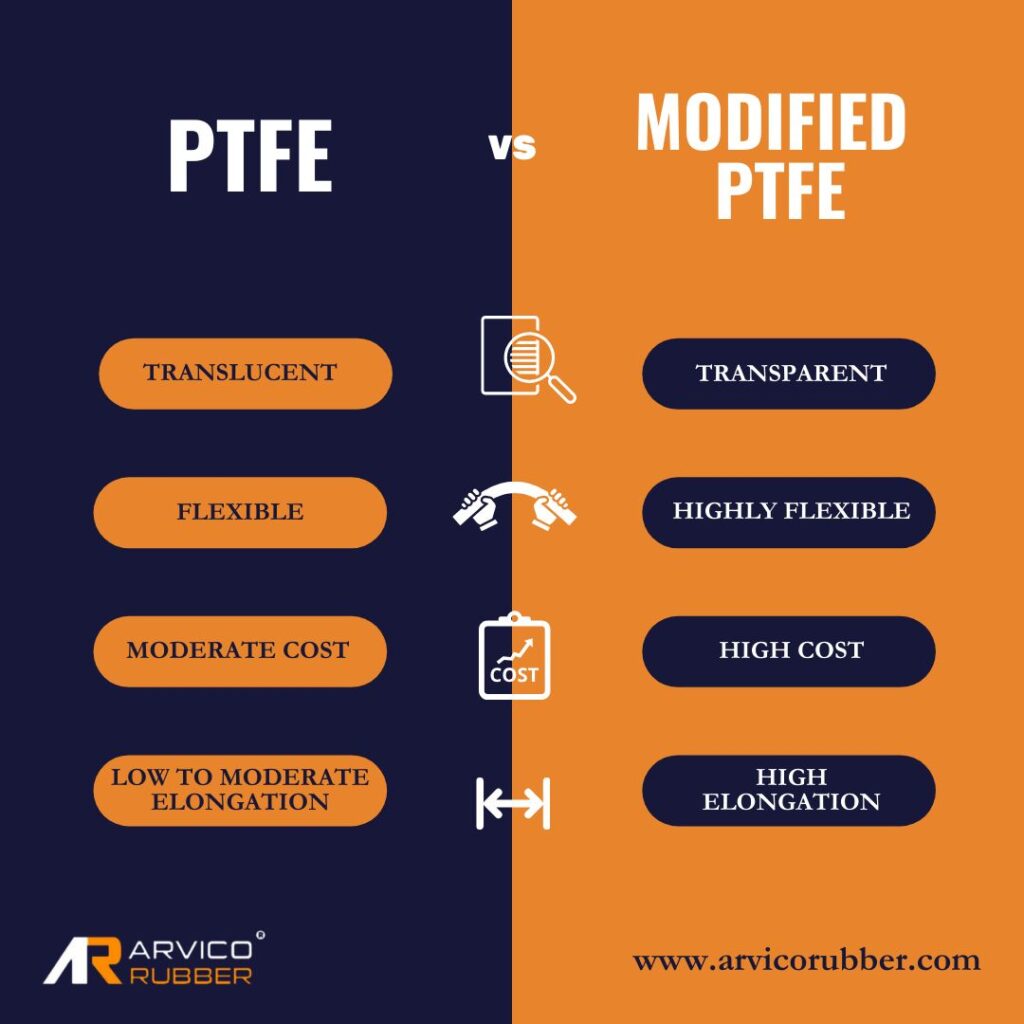
How to Change the Strength of Rubber?
Naturally, different types of rubber come with different tensile strengths. However, you can change the tensile strength of a particular polymer by mixing in different fillers with different chemical properties to the polymer while producing it.
Do remember that the tensile strength change with different scenarios. While in normal state, natural rubber has a higher tensile strength than silicone rubber, when these materials are heated, the tensile strength gap reduces between these two types of polymers.
How to Test the Tensile Strength of an Existing Rubber Component?
Let’s say you ordered a million pieces of rubber valves, and the rubber component manufacturer gave you some samples to check out.
It is important for your team to find the tensile strength of rubber used in making the component before giving the go-ahead for the rest of the component manufacturing.
The easiest way to do this is to use either the dumbbell cut-out test or the ring cut-out test. A small part of the component can be cut or molded into either of these shapes, and the tensile test can be conducted.
If possible, ask the manufacturer for a raw piece of the polymer to conduct the test, which may give more accurate results. It is always recommended to get the tensile test done and not depend on the values that the manufacturer mention, especially when the order is large.

Takeaways
Knowing the strength of the rubber used in creating your components will help you use the component in an effective manner. While higher tensile strength is usually considered beneficial, you need to remember that polymers with high tensile strength may have other limitations, like a high oxidation rate or being erosion-prone.
We at Arvico Rubber start all client discussions with a clear mention of all essential features of the polymer of choice, including its tensile strength. We can also help clients choose the right polymer from the different types of rubber materials that we offer, depending on their component usage and specifications.
If you would like to know more about tensile strength of rubber and other component offerings and our success stories, please get in touch with us at info@arvicorubber.com. You can also check our expansive product portfolio online and place orders for custom-engineering products of different specifications.