Arvico Rubbers is one of the few Indian brands that understand the customers’ needs perfectly well and design rubber components that are precise, perfect, and match the requirements 100%. One such component we create is expansion joints rubber.
Here is everything you need to know about expansion joints.
Expansion joints give physical reinforcement to components in industrial settings. In industrial environments, vibrations, misalignments, and unplanned parts movements can cause problems in the normal functioning of the system. Such movements and vibrations can also damage expensive equipment with time.
Expansion joints are added to such joints to ensure the vibrations and movements are dampened.
Why are Vibrations and Movements Bad?
This is a question you may have while talking about expansion joints. Why are vibrations and movements bad in industrial settings? Why does one need to invest in these tiny rubber components?
- Vibration hazards are huge in workplaces. Machine vibrations can cause physical injuries to people working in the units.
- Vibrations also cause friction and lead to physical damage to expensive equipment and machines.
- In hand-held machines, physical vibrations can actually reduce blood flow in the palms and hands, and this can lead to long-term damage.
- Vibrations and movements also cause noise pollution in industrial setups.
A humble expansion joints rubber can help get rid of all these problems instantly, and that is why these are best sellers in Arvico Rubber.

Types of Rubber Expansion Joints
There are so many types of rubber expansion joints, depending on their design and usage.
- Single arch type – This type has a single arch in the middle and a full-face flange design.
- Multiple arch type – This has multiple arches in the center portion, and the arches can come together to form a tight seal that the single arch type cannot provide.
- Taper type – In this style, the expansion joints are tapered. That is, they have varying diameters on both ends of the joints and are connected by pipes.
- Offset type – If there is a misalignment in your setup, then your expansion joints manufacturer will create an offset type expansion joint that can rectify the alignment issues.
- Sleeve spool type – A sleeve pool type can slip over pipes and are to be secured with clamps. These are also available in single and multi-arch types.
- Enlarged end type – As the name suggests, one end of the expansion joint is enlarged than the other end.
- Integral Flange type – This model with a longer radial arch can be designed with both single and multiple arches. These are perfect for moving with the parts, along with providing reinforcements.
When it comes to Arvico’s products, you can choose between three variants – expansion joints with single, double, and triple arch joints. Also, these joints can be designed with or without flanges. Flanges are protruding rims or lips that help with easy connectivity and better strength.

Uses of Rubber Expansion Joint Rubber
Now, as an expansion joints manufacturer, we recommend the below kinds of usage of expansion joints.
- To fix misalignments in pipes
- To absorb vibrations, compressions, and expansions
- To handle excess pressure loads in joint areas
- To create isolation and reduce noise
- To improve the lifespan of piping systems and other equipment
- To help bring down the stress on equipment flanges
- To bring down stress on the general working system.
Applications of Rubber Expansion Joints
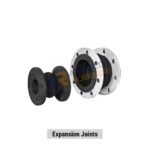
There are so many areas where an expansion joints rubber can be used. Some of them are:
- HVAC devices
- Piping systems
- Desalination plants
- Power plants
- Ducting systems
- Chemical industries
- Pharmaceutical industries
- Refineries
- Compressors
- Sugar industries
- Marine industries
- Wood-processing industries
How Should an Expansion Joints Manufacturer Design an Optimal Expansion Joint?
- Using high-tech, state-of-art design
Without a doubt, the first thing that is needed for an expansion joints manufacturer to do is to create an efficient and high-end model. This starts with using the right skilled workers, having the right setup to create products, and having quality check processes in place.
Did you know that all products from Arvico Rubber go through multiple quality check processes, both internal and external? We are certified by multiple organizations, and our product quality speaks for itself.
- Choosing the right material
You can choose to produce expansion joints in a variety of materials, including natural rubber, nitrile rubber, neoprene rubber, butyl rubber, EPDM rubber, and silicone rubber, to name a few.
Here is a blog that talks about EPDM rubber and its applications and uses that you can read next.
Now, each of these materials has its own advantages, and the lighter the material you choose, the more flexible the joint will actually be. If you are picking expansion joints to use under high-pressure situations, then materials with high tensile strength like polyurethane rubber, EPDM rubber, or nitrile rubber are good choices. You can talk to your expansion joints manufacturer to understand these differences.
- Picking seamless design
According to experts, an expansion joint rubber that has overlapping plies and seams cannot function with 100% efficiency. That is why designing them in seamless layers is very important. The right manufacturer, like Arvico Rubber, can do this effectively, thanks to our 55+ years of experience.
- Opting for the best design quality
Our team spends a considerable part of the production process around a table, designing the perfect component for your use. Since most of our clients approach us for custom-built expansion joints, we take great care in designing them right. As a result, the product fits their needs perfectly and serves the purpose. Our design software and the molding unit work together, helping customers get the right product every time.
- Investing in thorough quality checks
We understand that quality is everything for customers, and that is why products from Arvico go through multiple quality checks before reaching you. As an expansion joints manufacturer, we assure the below quality testing facilities for our customers, for any component that they choose.
- Hardness Testing
- Tensile Strength Testing
- Compression Strength Testing
- Ozone Testing
- Dimensional Checking
- Finish and Visual Checking
- Spark Testing
- Flex Testing
Advantages of Rubber Expansion Joints
Below are the advantages of using flexible expansion joints rubber.
- Expansion joints are easy to install. You don’t have to spend additional effort or skills installing rubber joints.
- A cheaper way to minimize vibrations, noise, and friction.
- Very protective against high-pressure points. These rubber expansion joints may look tiny but can handle pressure and stress like a pro when designed with the right material.
- Flexible design – Want a really small expansion joint in millimeters? Yes, that can be done. Want an expansion joint to fit a 30-inch pipe? That can be done too. With the right rubber expansion joints manufacturer, you can design these components in any size and shape you want.
- These expansion joints can protect from heat loss too, which is an added advantage.
- Rubber expansion joints, in the right materials, can be corrosion and erosion-resistant too.
Conclusion
An expansion joints rubber from our brand can be used in a variety of industries to absorb vibration, movements, and misalignments. Depending on the specific purpose of use, you can design the expansion joint with or without flanges.
Confused whether to choose single, double, and triple arch joints? Talk to our experts to know which model will fit your needs right.